组委会联系方式
电话:4006-258-268
烘干展官网:www.apdrying.com
亚洲供热展:www.heat-ahe.com
办公地址:广州市海珠区新港东路保利世贸中心西塔C座7《鸿威集团》
疫情之后农业烘干必将增长!来看这10个热泵烘干省钱案例!
2020年的疫情猝不及防,不要说对空气能行业,对中国经济的冲击都会非常大。但是就空气源热泵行业来说,今年一定会增长的肯定是农业烘干!
这里有两个逻辑支撑,第一个点,政府的三大攻坚战,脱贫是排名第一的,而且今年这个指标是完成也要完成,不完成也要完成的。因此对农村和农业生产加工的补贴必将加大。
第二个,空气源热泵烘干,节能效果显著,能帮客户省钱就是赚钱。这在经济困难阶段更加弥足珍贵。只要把项目做好,适当创新一下商业模式,农业烘干市场前途非常大!
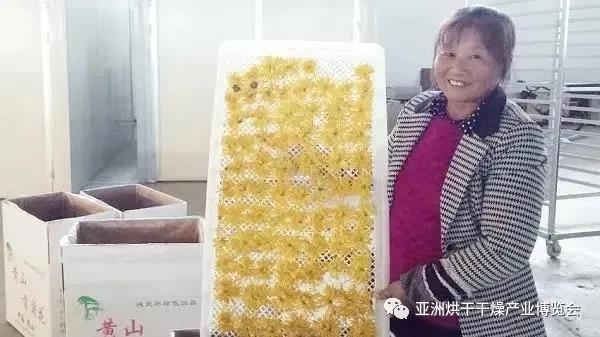
热泵烘干技术具有能源消耗少,环境污染小、烘干品质高、适用范围广等优点,其优异的节能效果已被国内外的各种试验研究所证明。下面,让我们通过十个实际案例来看看热泵烘干相对于烧柴、燃煤、燃油、电加热等方式烘干的节能性。
四川无花果烘干原来采用燃煤和燃油等方式烘干,后来采用空气能热泵高温除湿机烘干,在整个烘干和除湿过程中采用智能热回收,使能源利用率大大提高,综合节能效果明显高于其他烘干方式。
能源运行费用分析表(以燃油锅炉为例):
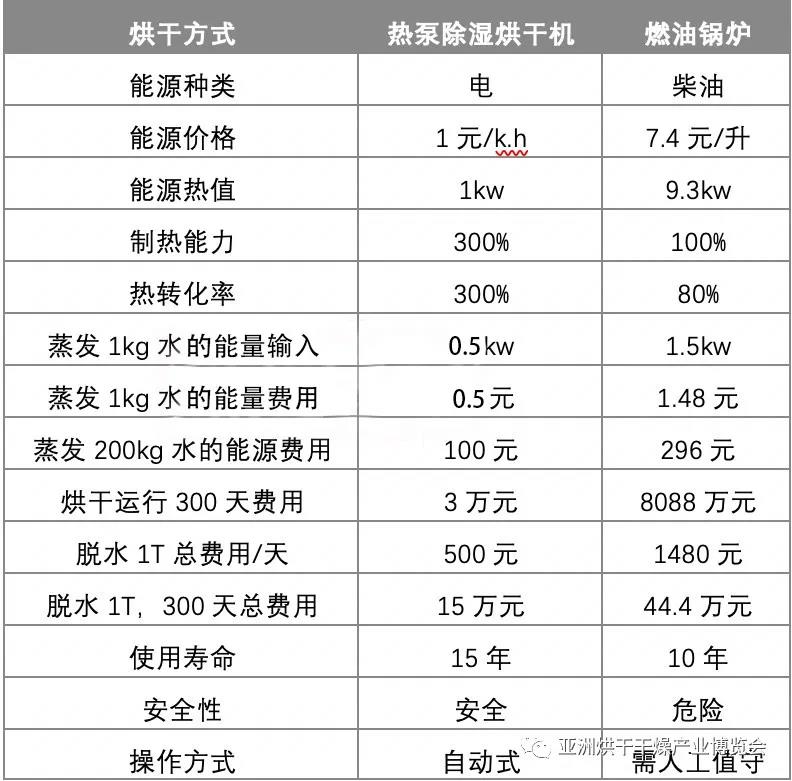
(图片来源:热泵市场)
从上表运行费用分析可知:虽然空气能热泵烘干机投资较大,但其节能效果明显、安全性高、操作简单无需人工值守,初投资费用可在后续的运行费用中回收,回收期限小于两年。空气能热泵烘干整年运行费用每年节省29.4(44.4万~15万)万元。
浙江某纸品加工厂采用热泵烘干,八条独立的生产流水线,每条流水线配备一台10P空气能烘干机和两台内机,每条纸管流水线平均每天运行10个小时,电费0.9元/度,每套空气能热泵烘干机平均电费大约在80元/天。
同样情况下,之前单纯用电热管烘干,电费大约为180元/天。而根据市场调查,燃烧生物质颗粒的成本大约为90元/天。由此可见,热泵烘干在运行费用方面优势明显。
项目为深圳市某通信公司,为手机等通讯部件提供空气源高温加热电镀。运行费用:(按每天运行18小时计算,电费0.5元/度),每天总的运行费用:(5×2+6.3×7+11×7+3×2+6.5×5+4.5×2)×18×0.5=1607元,年运行费用: 1607×30×12=578520元。
原来使用电加热的运行费用:电加热每天的运行费用:1607×2=3214元,则每年的运行费用为: 3214×30×12=1157040元,使用高温热型热泵为使用电加热节省的费用的1/2。
山东德州新县某蝴蝶面加工厂,每天10小时生产2250公斤干品蝴蝶面。以前采用燃煤锅炉,平均每天耗煤0.35吨,合260元,加上堆煤场每月租金、司炉工工资、锅炉年检、环保检查和其他灰色开支,实际上每月的干燥开支是19100以上。
改造后采用热泵干燥,每天的干燥成本为:启用热回收机组(24KWX10小时+ 5KWX10小时)X0.8元/度=232元,不启用热回收机组24KWX10小时X0.8元/度=192元。
那么,一个月的总干燥开支为:启用热回收机组232X30=6960元,不启用热回收机组192X30=5760元。按照一年一半的时间启用热回收机组来计算,平均每个月的总干燥开支为(6960+5760)/2=6360元,那么改造后平均每月创造的经济效益:19100元-6360元=12740元。
贵州某食品加工企业被全球500强第一的沃尔玛超市选定为中国区全国联采产品(全国只5个单品获选,贵州省仅一个单品获选),原来采用燃煤烘干,在政府限制煤锅炉使用的情况下,改为热泵烘干。
冬季气温低至-5℃,,每斤干品的成本只需要1.1元,远远低于之前燃煤的2.7元每斤,人工费用也减少了很多(燃煤干燥需要三次换车);干燥周期大大降低,由原来燃煤的30多个小时缩短至现在的14个小时。热泵干燥的产品颜色鲜艳,没有出现燃煤干燥出来的产品成暗褐色的情况,且口感更好。
本工程位于宁夏自治区吴忠市,根据客户的要求,建设空气源热泵+太阳能辅助的双源枸杞干燥系统,采用聚胺脂保温板制作烘干房,宁夏枸杞烘干系统烘干房尺寸为18.53m*7.15m*2.12m,总容积281 m³,每次可进入枸杞9000Kg。
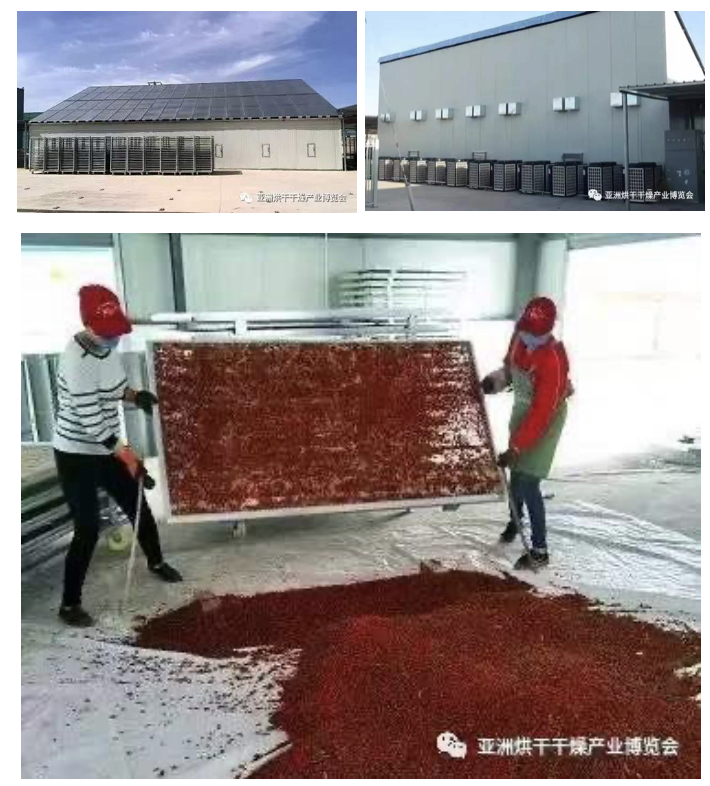
烘干房配置14台10匹空气源高温热泵烘干机和162㎡太阳能空气集热器。采用热泵+太阳能双源枸杞干燥系统的情况下与直接用电加热干燥房相比,每天约能节省9600度电。
该项目位于广州,将常温下的桶装化工原料放入烘房,烘干房尺寸为:长5.1m,宽1.5m,高2.8m。逐渐保存至目标温度55℃左右,最高不超过60℃,达到温度以后,再将化工原料从烘房里面取出,24小时不间断工作,每年工作时间250天。以前使用电热鼓风恒温干燥系统,电加热的功率是42KW,电价1.0元/度。每天的耗电量是280度。
改造后采用智能化整体式空气源热泵烘房设计,全天候充分满足甲方的化工原料保存需求,配置一台输入功率为6.0KW,制热量18KW的热泵烘干机组,每天的耗电量为144度。
广西桂林罗汉果烘干,原来大多采用柴火烘干窑,烘干时间较长,大火需要5~8天,小火则需8~10天,成本方面,柴火烘干(含人工成本)约为5~6分钱一个果。
采用热泵烘干后,只需要4~5天,成本只需要2.5~3分钱/个,比传统烘干成本少了一半。且提高了罗汉果的收购和市场价格,烘干窑干燥的罗汉果收购价约为0.9元/个,市场价约为1.2元/个;而热泵烘干的罗汉果收购价约为1.5元/个,市场价约为1.8元/个。
该项目位于河北某食品加工厂,日产量为10吨原料,2吨成品,原烘干方式为煤锅炉(政府正在取缔燃煤锅炉),烘干时间为20小时。
现有十个烘房全部改造成为热泵干燥,烘房的尺寸为6×4×2.5m,每次烘干果脯总量为1000公斤,【热泵市场 水印】配置了2台10匹的整体式烘干机。原来燃煤烘干每天的运行费用约700元,1度电按市价1元/度,而改造后热泵烘干每天运行费用仅为270元。
该项目位于湖南常德,项目采用20台13P的热泵烘干设备之前采用燃煤炉烘干,每千克烟的烘干成本为0.96~1.46元。
- 中通协召开流体机械展览会2014年首次专题工作会议[2015-11-8]
- 中通协展览部考察上海的展览会服务商[2015-11-8]